The double-roller casting and rolling method has simple equipment, low total investment, and short production cycle. It eliminates many tedious processes such as milling, homogenization, and hot rolling in the production of hot-rolled plates. Therefore, the casting-rolling method is more suitable for producing aluminum foil blanks. The cost is greatly reduced; however, due to the different cooling methods and hot processing conditions during the production of plates by the double-roll casting and rolling method, the internal structure of the cast-rolled plates mainly has shortcomings such as segregation, uneven structure, and coarse grain structure after annealing, and its quality control It is more difficult, so it is relatively rarely used in high-quality aluminum foil products.
At present, the process of casting and rolling applied to aluminum foil blanks is gradually maturing. More and more companies are beginning to use the casting and rolling process to produce aluminum foil. Casting and rolling have become the mainstream front-end process for aluminum foil. Casting and rolling appeared in the 1970s, and the technology is still not perfect.
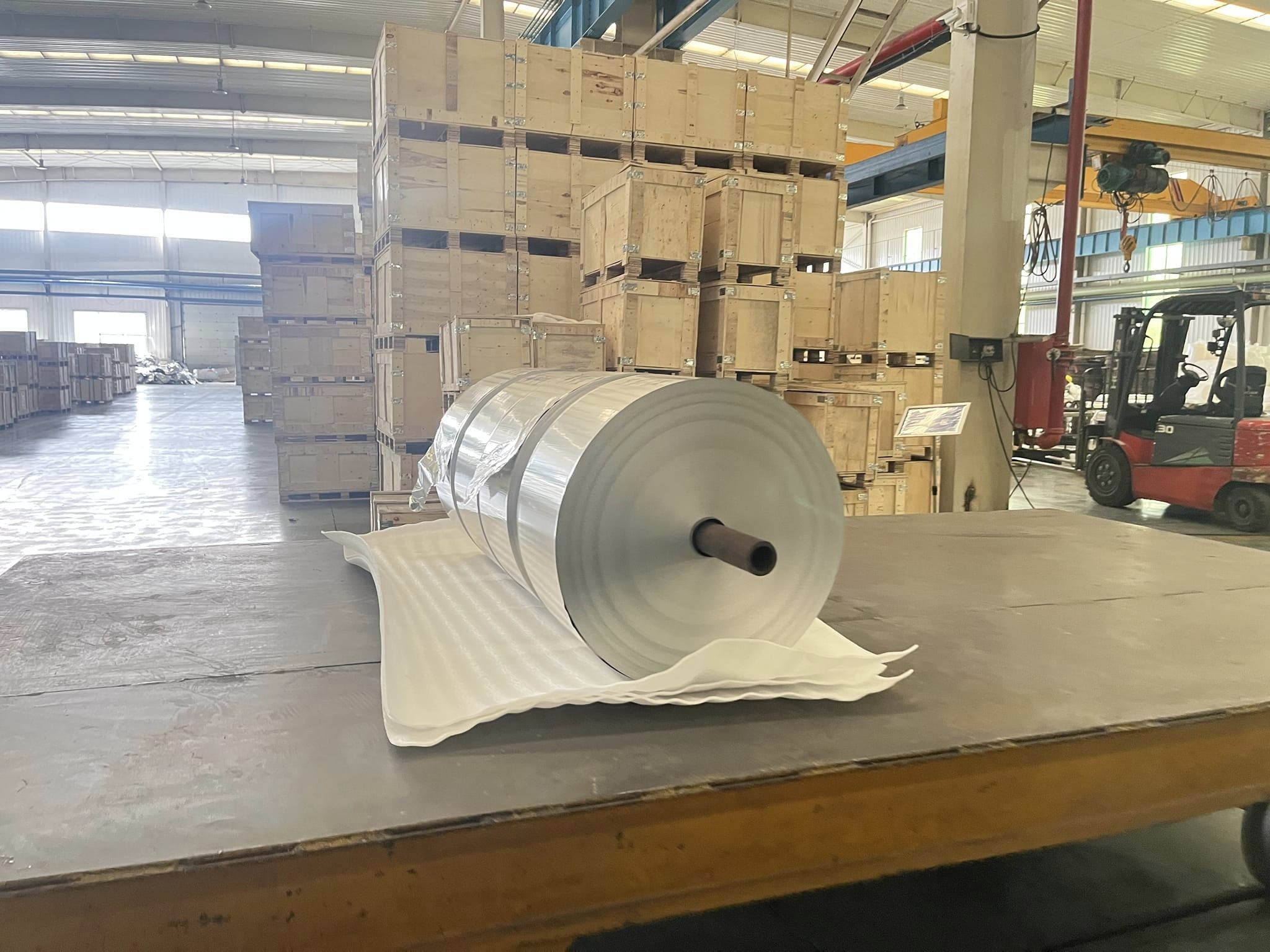
In recent years, Dingsheng New Materials has independently developed "casting-rolling-cold rolling short-process green manufacturing technology" and has successfully applied it to high-end products such as double-zero foil and power battery foil. This technology innovates the entire industry chain from composition optimization, smelting process, continuous casting and rolling process and cold rolling/foil rolling process optimization, as well as performance testing and quality control technology. It uses the casting and rolling method instead of the hot rolling method to produce aluminum foil for power batteries. / thin plates, which reduces the production costs of aluminum foil / thin plate manufacturers for power batteries, improves market competitiveness, and to a large extent promotes the development of the domestic battery aluminum processing industry.
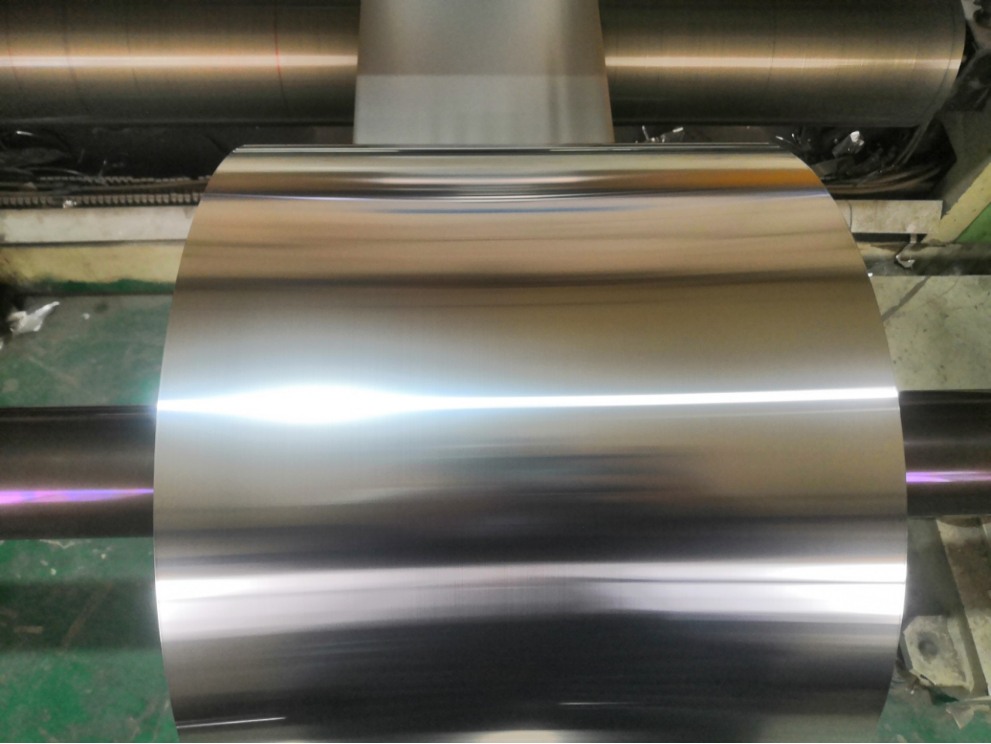
After the aluminum foil blank is made, the aluminum foil blank undergoes a series of rough rolling, intermediate rolling and finishing rolling into aluminum foil of different thicknesses, and then the finished product is annealed. Generally speaking, thick foil only needs to go through rough rolling, single zero foil needs to go through rough rolling and intermediate rolling, double zero foil and other aluminum foils with higher precision requirements need to go through rough rolling, intermediate rolling and finish rolling.
As far as the aluminum rolling industry is concerned, the hot rolling route is mostly used. According to China Nonferrous Metals News, as of the end of 2018, there were more than 800 double-roller casting and rolling production lines in China, with an annual production capacity of more than 8 million tons; there were more than 200 ingot hot rolling production lines, with a production capacity of about 20 million tons/year. By 2020, China's twin-roll continuous cast-rolling strip production will exceed 8 million tons, and the ingot hot-rolled strip production will exceed 42 million tons per year.