The aluminum foil processing process is the aluminum product with the most processing steps, the smallest thickness, and the most difficulty in the aluminum processing industry. There are currently two commonly used processing routes in the industry:
(1) Ingot hot rolling method; (2) Double-roller casting and rolling method.
Ingot hot rolling method
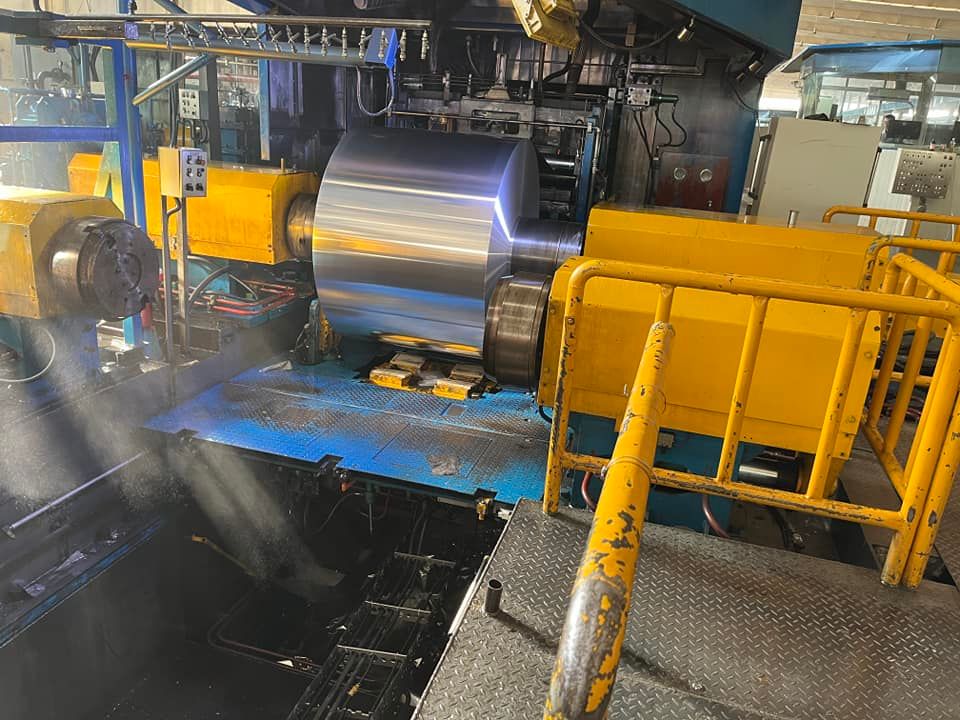
First, the aluminum melt is cast into a flat ingot, and then after homogenization, hot rolling, cold rolling, intermediate annealing and other processes, it is continued to be cold rolled into a plate with a thickness of about 0.4~1.0 mm as a foil blank (casting → hot rolling) Billet→cold rolling→foil rolling).
In the ingot hot rolling method, the hot-rolled billet is first milled to remove defects such as the oxide layer and impurities on the surface of the ingot, and then the microstructure of the ingot is made more uniform through homogenization, and then hot rolling, cold rolling and intermediate After multiple processes such as annealing and recrystallization, the internal structural uniformity and grain size of the billet have been significantly improved. Therefore, hot-rolled billets are usually of better quality and are suitable for high-quality double-zero aluminum foil and deep processing. Aluminum foil products. However, hot-rolled blanks have problems such as high ear yield, easy cracking, and uneven deformation areas during the deep drawing process, which restricts the improvement of the yield of high-quality aluminum foil.
Two-roll casting method
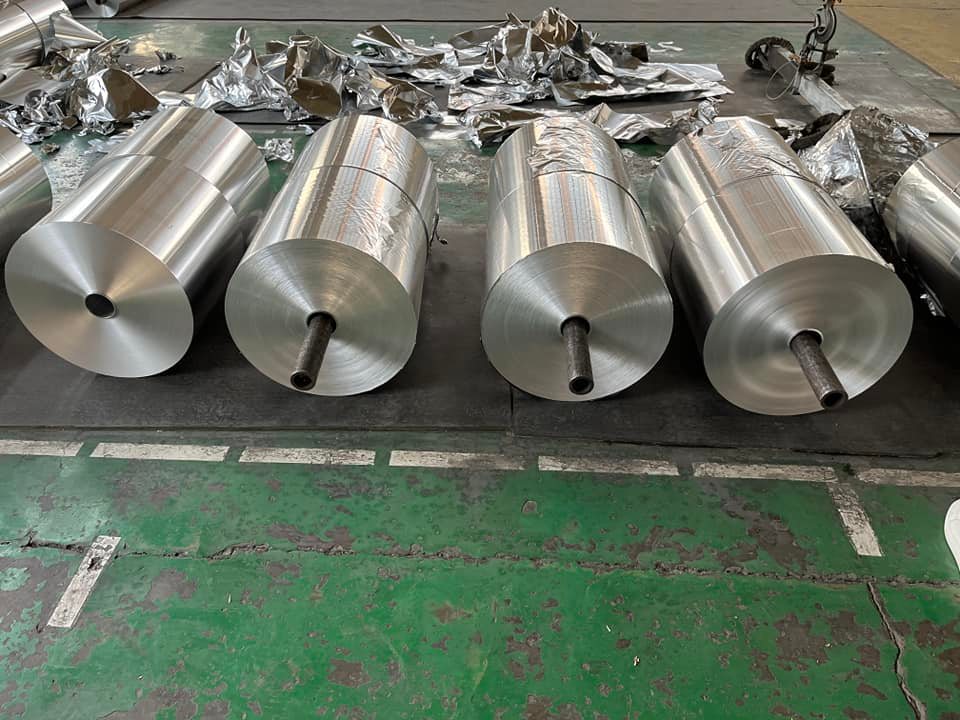
Compared with the ingot hot-rolling method, the process flow of producing aluminum foil blanks by the cast-rolling method is relatively simple; there is no need to go through complex process steps such as ingot melting, milling, homogenization and hot rolling, but the aluminum melt is poured directly. Enter two rotating casting rollers (crystallizer), and complete the solidification and hot rolling processes simultaneously in the casting and rolling area within 2 to 3 seconds to obtain a plate with a thickness of 4 to 7 mm. Similar to hot-rolled aluminum foil billets, cast-rolled plates also need to go through a series of cold rolling and intermediate annealing processes, and are finally rolled into 0.3~0.7mm thick plates as aluminum foil billets.